Plastic extrusion for strong and lightweight components
A Comprehensive Guide to the Process and Benefits of Plastic Extrusion
In the huge world of production, plastic extrusion becomes a essential and extremely efficient procedure. Translating raw plastic into constant profiles, it caters to a variety of industries with its impressive flexibility. This overview aims to clarify the complex steps associated with this technique, the sorts of plastic apt for extrusion, and the game-changing benefits it gives the sector. The occurring conversation promises to unfold the real-world impacts of this transformative procedure.
Understanding the Fundamentals of Plastic Extrusion
While it may show up complicated in the beginning glance, the procedure of plastic extrusion is basically straightforward - plastic extrusion. It is a high-volume manufacturing method in which raw plastic is melted and formed into a constant account. The procedure starts with the feeding of plastic product, in the form of granules, pellets, or powders, right into a warmed barrel. The plastic is after that thawed making use of a mix of warmth and shear, applied by a turning screw. Once the molten plastic gets to completion of the barrel, it is required through a small opening referred to as a die, forming it right into a wanted form. The designed plastic is after that cooled down, solidified, and cut right into desired lengths, completing the process.
The Technical Process of Plastic Extrusion Explained
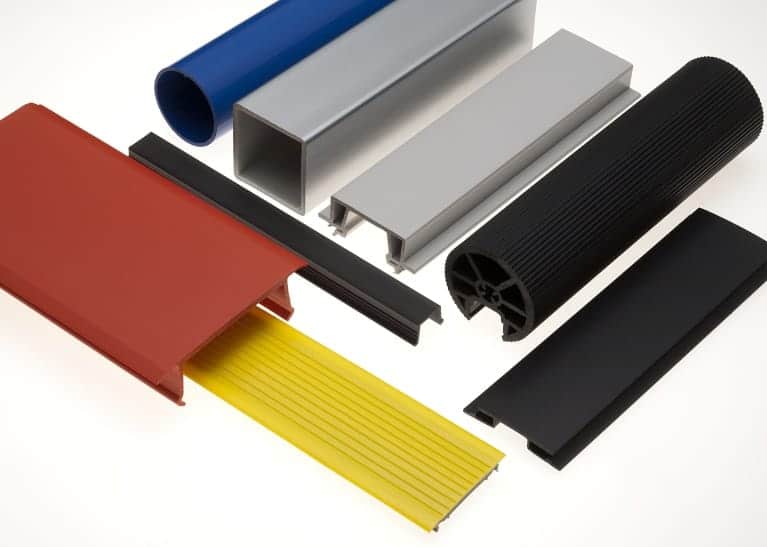
Sorts Of Plastic Suitable for Extrusion
The choice of the appropriate kind of plastic is a crucial element of the extrusion procedure. Various plastics supply distinct residential or commercial properties, making them more fit to specific applications. Comprehending these plastic types can substantially improve the extrusion procedure.
Comparing Plastic Extrusion to Various Other Plastic Forming Techniques
Recognizing the types of plastic appropriate for extrusion leads the way for a broader discussion on how plastic extrusion stacks up versus various other plastic developing techniques. These consist of shot molding, impact molding, and thermoforming. Each approach has its one-of-a-kind usages and advantages. Shot molding, for instance, is superb for producing detailed parts, while strike molding is ideal for hollow objects like bottles. Thermoforming excels at developing superficial or huge components. Plastic extrusion is unrivaled when it comes to producing continuous accounts, such as pipes, seals, and gaskets. It likewise permits a regular cross-section along the size of the item. Thus, the selection of approach greatly depends upon the end-product requirements and specs.
Key Benefits of Plastic Extrusion in Manufacturing
In the realm of manufacturing, plastic extrusion uses many considerable advantages. One significant advantage is the cost-effectiveness of the process, which makes it an economically enticing manufacturing method. In addition, this strategy offers superior product versatility and improved manufacturing rate, thereby increasing general production performance.
Cost-efficient Production Technique
Plastic extrusion leaps to the leading edge as a cost-effective manufacturing method in manufacturing. This procedure sticks out for its capacity to generate high quantities of product rapidly and effectively, offering manufacturers with considerable financial savings. The main cost advantage is the ability to make use of cheaper resources. Extrusion uses thermoplastic products, which are much less expensive compared to porcelains or metals. Additionally, the extrusion procedure itself is fairly easy, lowering labor prices. In addition, plastic extrusion requires much less energy than conventional production methods, adding to reduced operational expenses. The procedure likewise reduces waste, as any kind of faulty or excess materials can be recycled and recycled, supplying one more layer of cost-effectiveness. On the whole, the financial benefits make plastic extrusion a highly eye-catching alternative in the manufacturing sector.

Superior Item Flexibility
Past the cost-effectiveness of plastic extrusion, one more significant benefit in manufacturing hinge on its remarkable product adaptability. This procedure enables for the development of a broad range of products with differing designs, sizes, and forms, from straightforward plastic sheets to detailed profiles. The versatility is associated to the extrusion die, which can be tailored to yield the preferred product design. This makes plastic extrusion an ideal option for markets that call for customized plastic elements, such as auto, building, and product packaging. The ability to create diverse items is not just valuable in conference certain market needs yet additionally in allowing suppliers to explore new line of product with very little capital expense. Fundamentally, plastic extrusion's item adaptability fosters innovation while improving operational performance.
Improved Production Speed
A significant advantage of plastic extrusion click to read depends on its boosted manufacturing rate. This production procedure enables high-volume production in a reasonably brief time period. It can generating long, constant plastic accounts, which substantially lowers the manufacturing time. This high-speed production is especially useful in sectors where big quantities of plastic components are needed within tight target dates. Couple of various other production processes can match the rate of plastic extrusion. Furthermore, the capacity to preserve consistent high-speed manufacturing without compromising item high quality establishes plastic extrusion besides various other techniques. The enhanced production speed, as a result, not only allows manufacturers to meet high-demand orders but likewise adds to boosted effectiveness and cost-effectiveness. This advantageous function of plastic extrusion has actually made it a recommended option in numerous markets.
Real-world Applications and Influences of Plastic Extrusion
In the world of manufacturing, the technique of plastic extrusion holds extensive significance. This procedure is widely made use of in the production of a variety of items, such as plastic tubing, window frameworks, and weather condition removing. Consequently, it greatly influences sectors like construction, packaging, and automobile industries. Its impact prolongs to everyday products, from plastic bags to tooth brushes and disposable flatware. The economic advantage of plastic extrusion, mainly its economical and high-volume outcome, has reinvented production. Nevertheless, the ecological impact of plastic waste continues to be a problem. Consequently, the industry is constantly pursuing advancements in biodegradable and recyclable materials, indicating a future where the benefits of plastic extrusion can be preserved without compromising ecological sustainability.
Final thought
In final thought, plastic extrusion is a highly find out reliable and reliable technique of changing resources into varied products. It supplies many benefits over various other plastic creating methods, including cost-effectiveness, high result, minimal their explanation waste, and layout flexibility. Its impact is profoundly felt in numerous markets such as building and construction, automobile, and durable goods, making it a critical process in today's manufacturing landscape.
Diving deeper right into the technological process of plastic extrusion, it begins with the choice of the ideal plastic material. As soon as cooled down, the plastic is cut right into the called for sizes or injury onto reels if the product is a plastic film or sheet - plastic extrusion. Comparing Plastic Extrusion to Various Other Plastic Forming Methods
Comprehending the types of plastic ideal for extrusion leads the method for a wider conversation on just how plastic extrusion piles up against various other plastic developing techniques. Couple of various other manufacturing procedures can match the rate of plastic extrusion.